The Essential Role of Car Parts Mold in the Automotive Industry
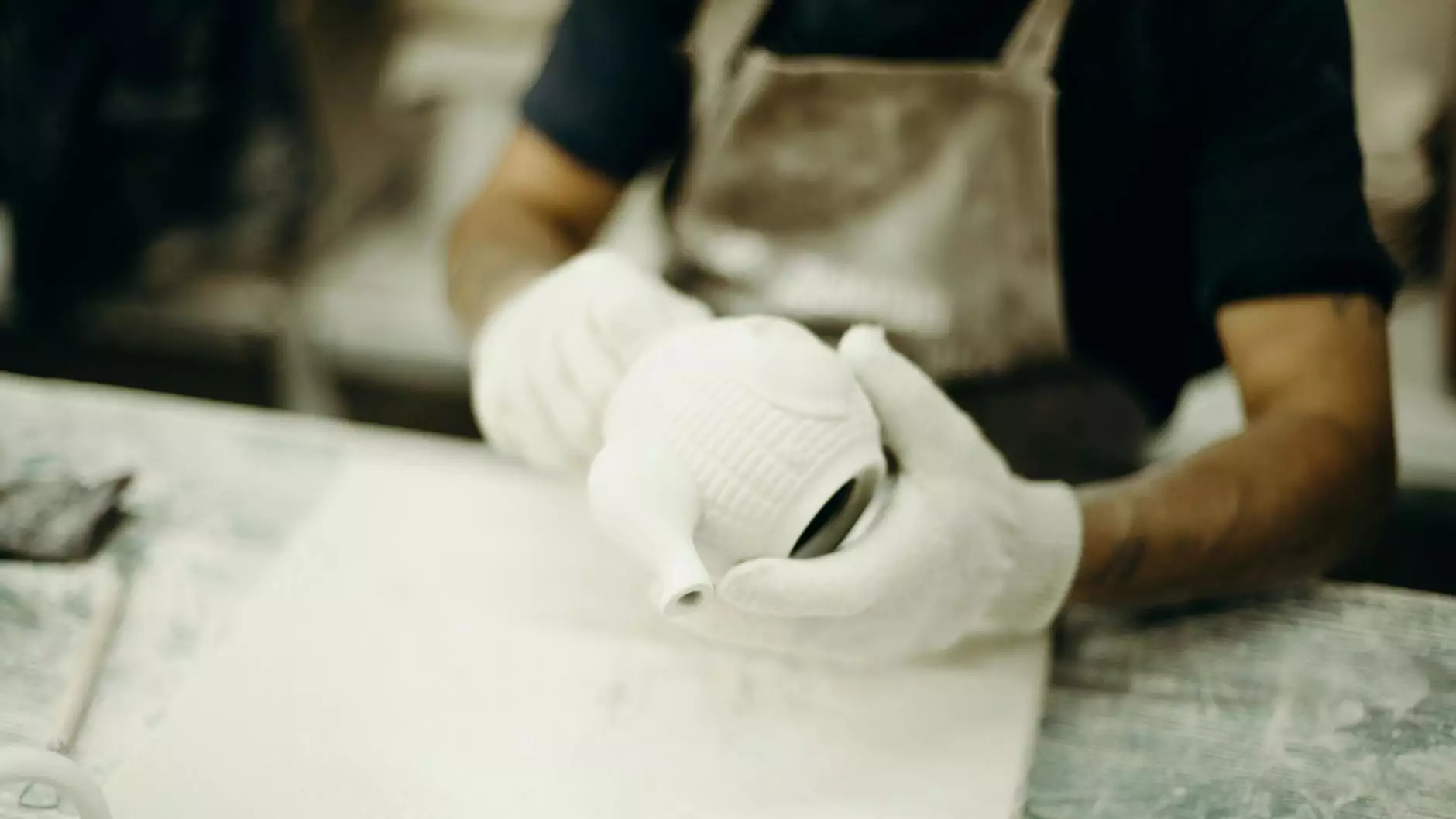
Car parts mold is a critical aspect of the automotive manufacturing process. Understanding the intricacies of mold-making allows manufacturers to produce high-quality components consistently. This article dives deep into various facets of car parts molds, their manufacturing processes, and how they contribute to the efficiency and innovation of automotive production.
What is Car Parts Mold?
The term car parts mold refers to the various types of molds used to fabricate components for vehicles. Molds are essential tools in manufacturing that enable the production of identical parts through processes such as injection molding, compression molding, and blow molding. The precision and quality of molds directly impact the durability and functionality of automotive parts.
The Importance of Quality in Car Parts Mold
Investing in car parts mold can significantly affect the manufacturing process and final product quality. There are several reasons why high-quality molds are vital:
- Durability: Quality molds are designed to withstand high-pressure conditions and repeated use without degrading.
- Cost-efficiency: Well-made molds reduce the waste of materials and energy during production, leading to lower operational costs.
- Precision: High-quality molds ensure that every part produced meets rigorous specifications, reducing the likelihood of rework or replacements.
- Innovation: Advanced mold technology enables the production of intricate designs and complex geometries that meet modern automotive demands.
Types of Car Parts Molds
There are several types of molds used in the automotive industry, each serving different purposes in the manufacturing process. Here are the most common types:
1. Injection Molds
Injection molds are perhaps the most widely used in the production of car parts mold. This process involves injecting molten material (often plastic) into a mold cavity, where it cools and hardens into the desired shape. Injection molding is renowned for its ability to produce complex shapes quickly and efficiently, making it ideal for high-volume production.
2. Compression Molds
Compression molding is another technique used to create car parts. In this method, a pre-measured amount of material is placed in a heated mold cavity. The mold is then closed, and pressure is applied to shape the material. Compression molds are commonly employed for rubber and thermosetting plastic parts.
3. Blow Molds
Blow molding involves creating hollow parts, which is particularly useful for items such as fuel tanks or air ducts in automobiles. This process requires a molten tube of material to be inflated within a mold, resulting in a variety of shapes and sizes that are lightweight yet durable.
The Car Parts Mold Manufacturing Process
Creating a car parts mold involves several critical steps, each of which requires precision and expertise. Here’s an overview of the typical manufacturing process:
- Designing the Mold: This initial stage involves computer-aided design (CAD) to create a digital model of the mold. Engineers and designers collaborate to optimize the shape and functionality of the mold.
- Material Selection: Selecting the right materials for both the mold and the components is essential for ensuring durability and functionality. Common materials include steel for long-lasting molds and aluminum for quicker production runs.
- Machining the Mold: The selected material is cut and shaped according to the design specifications. This step involves high-precision machining to achieve the required tolerances.
- Assembly: After machining, the various components of the mold are assembled, ensuring that all parts fit together seamlessly.
- Testing: Before the molds go into full-scale production, they are tested to ensure they meet quality standards. This may involve creating test parts to evaluate the mold's performance.
- Production: Once validated, the molds are ready for mass production, where they will consistently shape raw materials into car parts.
Challenges in Car Parts Mold Manufacturing
While the process of creating car parts molds seems straightforward, several challenges can arise that impact the quality of the molds and the final products:
- Rising Material Costs: Fluctuating prices of raw materials can significantly impact production costs.
- Technological Advancements: Staying abreast of the latest technology in mold-making is essential. Failing to invest in modern techniques may lead to inefficiencies.
- Quality Control: It’s critical to maintain high standards throughout the mold manufacturing process. Any lapse in quality can result in defective parts.
- Time Constraints: The pressure to reduce turnaround time can lead to rushed production, compromising quality.
Innovations in Car Parts Mold Technology
The automotive industry is ever-evolving, and so is the technology behind car parts mold. Innovations that are shaping the future of mold manufacturing include:
1. 3D Printing and Rapid Prototyping
3D printing technology allows for rapid prototyping of molds, enabling designers and engineers to create and test designs quickly, reducing time-to-market. This technology offers greater flexibility in mold design, making it easier to modify and improve designs based on practical feedback.
2. Advanced Materials
New materials with higher thermal stability and enhanced durability are being developed to withstand the rigors of the manufacturing process and improve the lifespan of molds. Using these advanced materials can lead to more efficient production and higher quality parts.
3. Smart Molding Technology
Smart molding technology integrates sensors and data analytics into the mold-making process, allowing for real-time monitoring and adjustments. This technological integration can significantly enhance precision and efficiency in the manufacturing process.
Why Choose DeepMould.net for Your Car Parts Mold Needs?
When it comes to selecting a reliable partner for car parts mold manufacturing, DeepMould.net stands out as a trusted metal fabricator. Here’s why:
- Expertise: With years of experience in the industry, our team of specialists understands the nuances of mold-making and automotive manufacturing, ensuring top-notch quality.
- Advanced Technology: We leverage the latest technologies in mold design and production to offer innovative solutions that meet the specific needs of our clients.
- Custom Solutions: Every automotive project is unique. We provide tailored solutions to address the specific challenges that each project presents, ensuring the best outcome.
- Quality Assurance: At DeepMould.net, we adhere to rigorous quality control processes, guaranteeing that every mold we produce meets the highest industry standards.
- Customer-Centric Approach: Our commitment to customer satisfaction drives us to provide exceptional service and support throughout the entire manufacturing process.
Conclusion
In conclusion, the role of car parts mold in automotive manufacturing cannot be overstated. Quality molds are indispensable for producing durable, high-performance vehicle components. As the industry continues to evolve, innovators like DeepMould.net are key to advancing mold technology and maintaining the highest standards in automotive production.
Whether you are a manufacturer seeking reliable mold solutions or an automotive company aiming to enhance your production capabilities, investing in quality car parts mold and partnering with an expert like DeepMould.net will pave the way for success in your endeavors.