Precision CNC Turning Parts Factories: A Comprehensive Guide
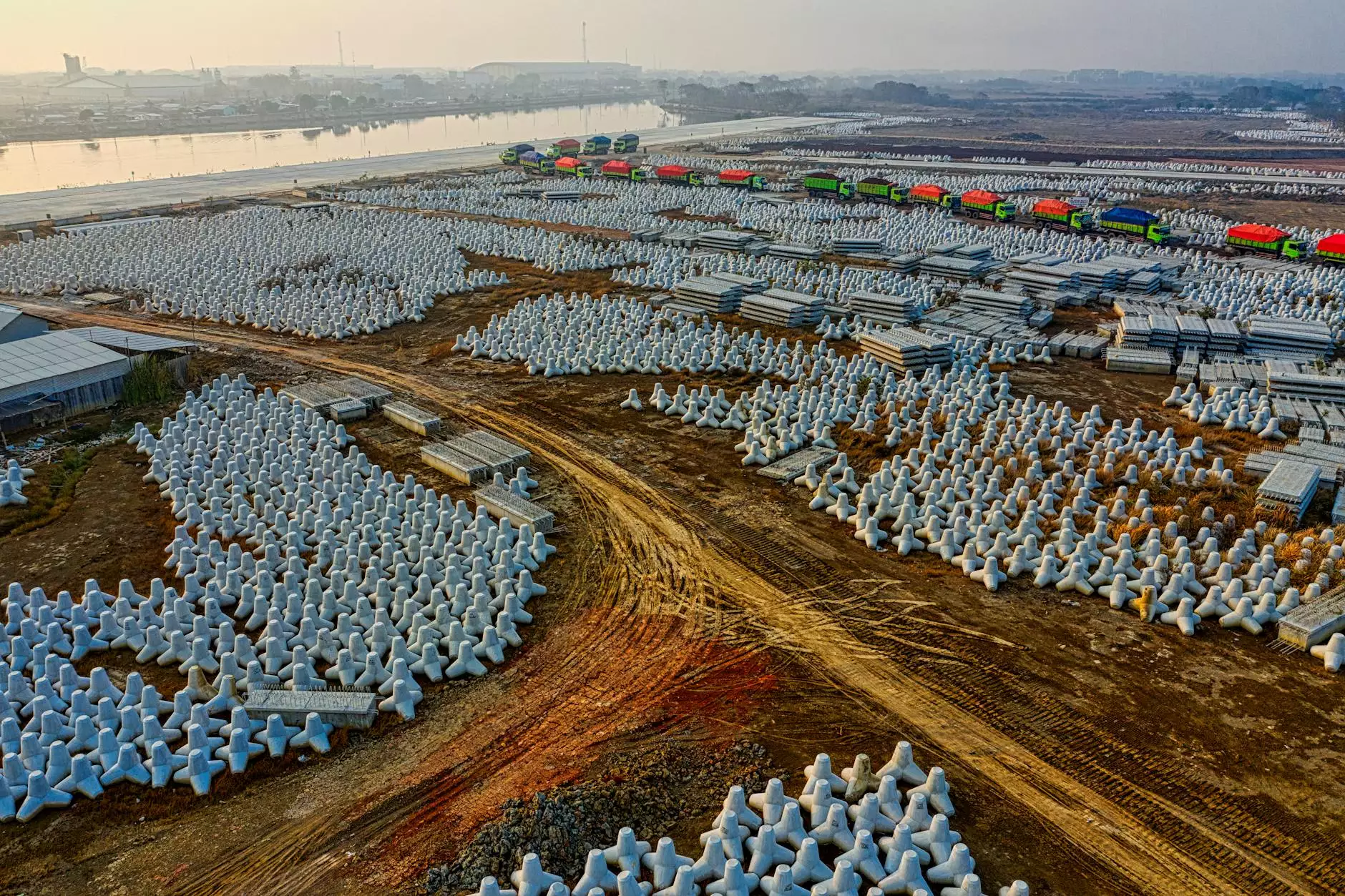
In today’s advanced manufacturing landscape, precision CNC turning parts factories stand at the forefront of metal fabrication technology. These factories utilize state-of-the-art machinery and high-level craftsmanship to produce components that adhere to stringent quality standards, serving various industries including automotive, aerospace, medical, and electronics. This article delves deeply into the intricacies of precision CNC turning, highlighting its significance, processes, and benefits, while focusing on how companies like DeepMould.net set themselves apart in a competitive market.
Understanding Precision CNC Turning
CNC turning, or Computer Numerical Control turning, is a machining process that involves rotating a workpiece while a stationary cutting tool removes material to create the desired shape. This process is vital for producing intricate parts with high precision and consistency. The evolution of CNC technology has enabled factories to operate with enhanced efficiency, resulting in plates and components that are not only precise but also cost-effective.
The Importance of Precision in CNC Turning
Precision in CNC turning is of paramount importance. Reasons include:
- Quality Assurance: Manufacturing parts that meet or exceed specifications ensures reliability and performance in the end-products.
- Reduced Waste: Higher precision means less material is wasted during production, leading to cost savings.
- Enhanced Performance: Quality parts perform better, ensuring the longevity and durability of the machines they belong to.
The Process of CNC Turning
The process of CNC turning involves several critical steps that ensure the highest quality results:
1. Design and Programming
Every CNC turning project begins with design and programming. Engineers use CAD (Computer-Aided Design) software to create precise digital models. These models are converted into CNC code (G-code) that instructs the turning machine.
2. Material Selection
Choosing the right material is crucial. Common materials used in CNC turning include:
- Metals: Aluminum, stainless steel, brass, and titanium are popular choices due to their mechanical properties.
- Plastics: Certain applications may require the use of durable plastics, which are also shaped effectively through CNC turning.
3. Machining
Once the material is selected, it is mounted on the CNC lathe. The lathe spins the workpiece at high speeds, while the cutting tool moves into contact with it, precisely shaping the component according to the programmed specifications.
4. Finishing
After initial machining, parts often require finishing processes such as sanding, polishing, or anodizing to enhance their surface quality and durability.
The Advantages of Precision CNC Turning Parts Factories
Precision CNC turning parts factories offer numerous advantages:
1. Scalability
These factories can produce small to large quantities of parts without compromising quality, making them suitable for both prototyping and mass production.
2. Automation
CNC machines can operate continuously with minimal human intervention, allowing for high throughput and reduced labor costs.
3. Flexibility
With the ability to handle various materials and design specifications, precision CNC turning factories can accommodate a broad range of projects across different industries.
4. Cost Efficiency
While initial setup costs may be high, the long-term cost savings achieved through reduced waste, high accuracy, and fast production times make CNC turning a cost-effective choice.
The Role of Quality Assurance in Precision CNC Turning
Quality Assurance (QA) is a vital aspect of precision CNC turning. Factories implement various measures to ensure the parts produced meet industry standards and customer expectations:
1. In-Process Inspection
During the machining process, periodic inspections ensure that dimensions remain consistent with specifications. This might involve using tools like calipers and gauges to measure critical dimensions.
2. Final Inspection
After production, every part undergoes a final inspection, which may include:
- Dimensional Checks: Verifying that the part meets the required specifications.
- Surface Finish Evaluation: Ensuring that the surface quality is suitable for its intended application.
- Functionality Testing: In some cases, parts are tested in their actual application to confirm they perform as intended.
Challenges Faced by Precision CNC Turning Factories
Despite the advantages, precision CNC turning factories face several challenges:
1. Technological Advancements
Staying current with rapidly evolving technology requires continuous investment in training and equipment.
2. Skilled Labor Shortage
The demand for skilled machinists and engineers is high, leading to a competitive job market that can challenge factories in recruiting the right talent.
3. Supply Chain Issues
Global supply chain disruptions can impact the availability of materials and components, hindering production schedules.
Industry Applications of Precision CNC Turning
Precision CNC turning is utilized across various industries:
1. Automotive Industry
In the automotive sector, parts such as engine components, transmission housings, and precision fasteners are manufactured using CNC turning processes.
2. Aerospace Sector
Aerospace applications require parts that can withstand extreme conditions. CNC turning is essential for creating components like landing gear parts and turbine housings.
3. Medical Equipment Manufacturing
CNC turning plays a critical role in producing precision parts for medical devices such as surgical instruments and orthopedic implants.
4. Electronics Industry
In electronics, CNC turning is utilized for high-precision connectors, housings, and mechanical components, ensuring reliable performance and safety.
DeepMould.net: Excellence in Precision CNC Turning
DeepMould.net is a leader in the field of precision CNC turning parts factories. With a commitment to quality and innovation, they utilize advanced CNC technology and maintain stringent quality control protocols to deliver superior products. Here’s what sets them apart:
1. Advanced Technology
DeepMould.net invests in the latest CNC turning machines and software, ensuring they remain at the forefront of technological advancement.
2. Expertise and Experience
The skilled team at DeepMould.net brings years of expertise to the table, ensuring that each project is handled with precision and care.
3. Comprehensive Services
From initial design to final delivery, DeepMould.net offers a full suite of services tailored to meet client needs, ensuring a smooth and efficient process.
4. Customer-Centric Approach
DeepMould.net prioritizes customer satisfaction, working closely with clients to understand their requirements and deliver results that exceed expectations.
Conclusion
In conclusion, precision CNC turning parts factories represent a crucial segment of the manufacturing industry, providing high-quality components that drive innovation across numerous sectors. Understanding the processes, advantages, and challenges associated with CNC turning is essential for businesses looking to leverage these services successfully. With industry leaders like DeepMould.net paving the way, the future of precision CNC turning is bright, promising advancements that will continue to enhance manufacturing efficiency and efficacy.
For any business or project needing precision CNC turning, choosing a reputed factory such as DeepMould.net is pivotal. Their commitment to excellence and quality ensures that you receive parts that not only meet but exceed your expectations in performance and reliability.