Revolutionizing Efficiency: The Art and Science of Industrial Blower Design
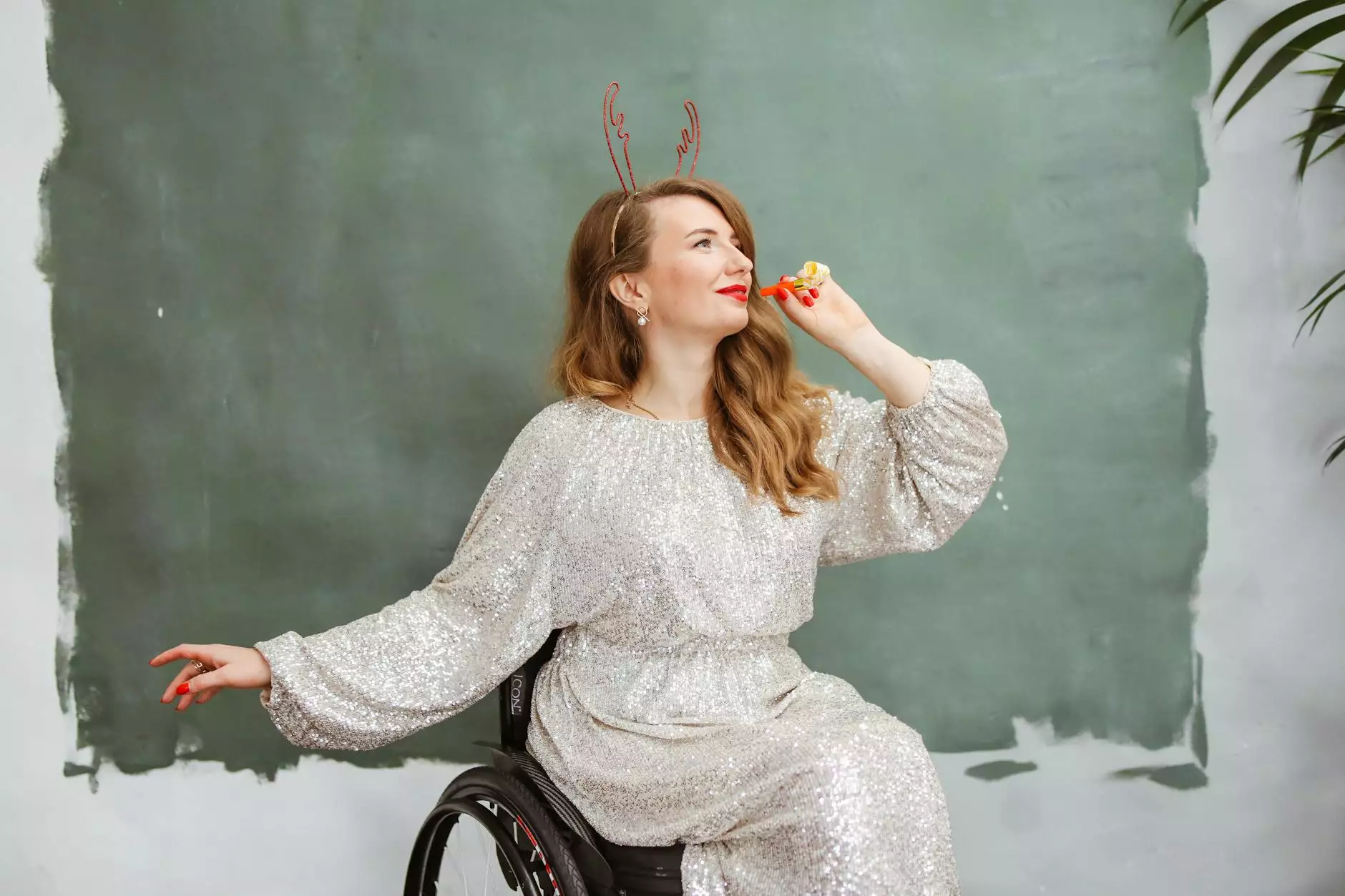
In today's fast-paced industrial landscape, having efficient air handling solutions is paramount. Among these, the design of industrial blowers stands out as a pivotal component that can significantly affect operational efficiency and energy consumption. This article delves into the intricacies of industrial blower design, offering valuable insights that can assist businesses in making informed decisions about their air management systems.
The Importance of Industrial Blower Design
The role of blowers in various industrial applications cannot be overstated. From ventilation and extraction systems to drying processes and material handling, blowers are integral to maintaining product quality and workplace safety. The proper design of these blowers directly correlates to:
- Energy Efficiency: Well-designed blowers consume less energy while maintaining optimal performance.
- Performance Optimization: Customized designs can meet specific operational requirements, enhancing overall efficiency.
- Longevity: A robust design prolongs the lifespan of blowers, reducing maintenance costs and downtime.
Understanding Key Concepts in Industrial Blower Design
To appreciate the nuances of industrial blower design, it is essential to understand several key principles:
1. Airflow Characteristics
The capacity of a blower is largely defined by its airflow performance. Factors that influence airflow characteristics include:
- Pressure Differential: The difference in pressure that the blower can create affects its ability to move air.
- Volume Flow Rate: This refers to the amount of air the blower can handle, measured in cubic feet per minute (CFM).
- Static Pressure: The resistance the blower faces while moving air through a duct system.
2. Blower Types and Their Applications
There are various types of industrial blowers, each designed for specific applications. The primary types include:
- Centrifugal Blowers: Known for their ability to produce high pressure, these blowers are often used in dust collection systems and pneumatic conveying.
- Positive Displacement Blowers: Ideal for applications requiring constant airflow, such as drying and cooling processes.
- Axial Flow Blowers: These blowers move air along the axis of the impeller and are typically employed in large volume ventilation requirements.
The Design Process of Industrial Blowers
Effective industrial blower design involves a systematic approach. Here is a detailed examination of the design process:
1. Requirement Analysis
The first step in designing an industrial blower is identifying the specific requirements of the application. This includes:
- Determining the necessary airflow rate.
- Understanding the operational environment and potential contaminants.
- Identifying factors like ambient temperature and humidity levels.
2. Component Selection
After gathering requirements, the next step is selecting appropriate components, which can include:
- Impeller: The design and material of the impeller influence efficiency and durability.
- Motor: Selecting a motor that meets the power requirements is crucial for performance.
- Housing: The blower housing design can affect noise levels and airflow consistency.
3. Computational Fluid Dynamics (CFD) Analysis
CFD simulations are employed to assess airflow patterns and performance metrics. These simulations help in refining the design before manufacturing. Key outputs from CFD analysis include:
- Velocity Profiles: Identifying high and low-velocity areas for optimization.
- Pressure Loss Predictions: Evaluating areas of potential inefficiency.
4. Prototyping and Testing
Once the design reaches maturity, creating a prototype is necessary. Testing the prototype under realistic conditions will help verify:
- Energy consumption against the expected output.
- Durability under continuous operation.
- Resistance to any environmental factors present in the operational setting.
Innovations in Industrial Blower Design
The field of industrial blower design is continually evolving, driven by technological advancements and the need for greater efficiency. Some notable innovations include:
1. Smart Blowers with IoT Integration
With the rise of the Internet of Things (IoT), smart blowers equipped with sensors can monitor performance in real-time. This technology allows for:
- Remote monitoring and diagnostics.
- Predictive maintenance to identify potential issues before they cause failures.
2. Energy Recovery Systems
Innovative designs now incorporate energy recovery systems that capture and reuse energy from the blowers, leading to:
- Significantly lower operational costs.
- Reduced carbon footprint for environmentally conscious industries.
3. Advanced Materials
Utilizing advanced materials in blower construction, such as composites, can enhance performance by:
- Reducing weight, which improves energy efficiency.
- Increasing resistance to corrosion and wear, leading to longer lifespan.
Case Studies: Successful Industrial Blower Implementations
To further illustrate the impact of effective industrial blower design, consider the following case studies:
1. Manufacturing Facility Upgrade
A prominent manufacturing facility upgraded its existing blowers, opting for advanced centrifugal blowers designed through CFD analysis. The results included:
- A 30% reduction in energy consumption compared to previous models.
- Improved product quality due to better temperature and humidity control.
2. Food Processing Plant Innovation
In a food processing plant, the implementation of positive displacement blowers allowed for:
- Consistent airflow during mixing processes.
- A reduction in moisture content variability, resulting in better product consistency.
Conclusion: Embracing the Future of Industrial Blower Design
The design of industrial blowers is a critical element in achieving operational excellence across various industries. As businesses continue to seek ways to enhance efficiency, reduce energy consumption, and improve product quality, investing in innovative blower designs becomes increasingly important.
By focusing on customization, technology integration, and ongoing development, companies like TMM can lead the way in delivering superior air management solutions that meet the demands of modern industrial environments. Embrace the opportunities that customized industrial blower design offers and position your business for success in a competitive landscape.
For further insights and expert advice on optimizing your industrial operations with cutting-edge blower technology, feel free to reach out to professionals in the field.